At Rhino, we’re committed to doing everything we can to support the wellbeing of our staff. We provide as many on-site resources as possible, and one of these resources is the Preventative Body Maintenance program.
We can all agree that it’s challenging to do a full day’s work when your body is filled with aches and pains, no matter what your job is. We don’t want our staff in pain, and we certainly don’t want their job to be causing pain. Injuries can be prevented if employees have on-site support to address their physical concerns, and the Preventative Body Maintenance program provides that support.
In 2006, we heard of Williston-based business Injury & Health Management Solutions (IHMS) ‘s work with other Vermont organizations, including Burton Snowboards and Vermont Teddy Bear. We quickly realized a partnership with IHMS was not only the solution for helping our staff who are hurting but a way to ensure their jobs weren’t adding to their injury. Since that year, they’ve supported us as an organization and as individuals to make sure Rhinos are as pain-free as can be through Ergonomics and Injury Prevention.
While we can’t have IHMS on site all the time (they’re juggling 50+ other Vermont organizations in over 100 locations!), the time they spend on site is incredibly impactful. When you walk into Rhino, you’ll see an IHMS schedule with a sign-up sheet for appointments. Those appointment slots are available three days a week to all Rhinos.
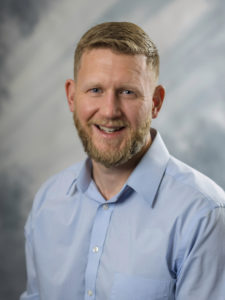
With a rotating three-person team, IHMS ensures they visit us often enough to know our staff by name. If appointment slots don’t get filled, it’s not unusual to see IHMS employees Charles, Joe, or Mike walking around the facilities to check in with everyone. In Charles’s words, ”We want to be a resource for all Rhino employees, human resources and safety when we’re are on-site. We take pride in being visible and active throughout the facility, whether in the warehouse, in production at RFDC, or in the office.” If Rhinos aren’t seeking out help, IHMS will seek out Rhinos. Rhinos are often caught off guard but pleasantly surprised when someone from IHMS approaches them during their shift and asks to take them off the floor for a follow-up.
More often than not, Charles finds that simply walking around the production floor will lead to Rhinos coming up to him with questions and concerns. IHMS makes themselves present; they show they’re invested in the wellbeing of the Rhino family, and that’s all it takes. Their dedication to our team doesn’t go unnoticed, and anyone at Rhino can confirm IHMS lives up to the “We care” slogan on the back of their business card.
Beyond one-on-one consultation and “a la carte” services, Charles and his team have assisted us in implementing changes that benefit everyone. Throughout the years, IHMS has worked with our team to identify ergonomic places for improvement throughout the facility.
Additionally, when Rhinos are hired, IHMS participates in new employee orientation to ensure employees have proper injury prevention and mechanics knowledge. Charles says that with their recommendations fully implemented, “Rhino Foods, as an employer, has done a tremendous job improving the ergonomics throughout the facility to reduce the physical requirements that employees have to perform. At this point, ergonomic concerns are most times not related to the job that needs to be done but rather due to the way employees choose to do the task. I feel we really bring value by being on the floor with employees helping them understand how to use their bodies and safely perform the job through job coaching. Especially in cases where the employee is reporting discomfort related to a job task.”
A big thank you to Charles and the IHMS team for all their work for our Rhino family! If you’re a Rhino, be sure to say hi to them and utilize this incredible on-site resource. Thanks to this partnership, we look forward to many more years of pain-free workdays!